Help found team in 2011
10th place overall finish 2012
4th place overall finish 2013
5th place overall finish, 1st place dynamic events 2014
Student-run, multi-disciplinary design team focused on designing and manufacturing a hybrid race car
Front powertrain driven with two independent electric motors, rear powertrain driven with 250cc engine
Annual national competition at New Hampshire Motor Speedway
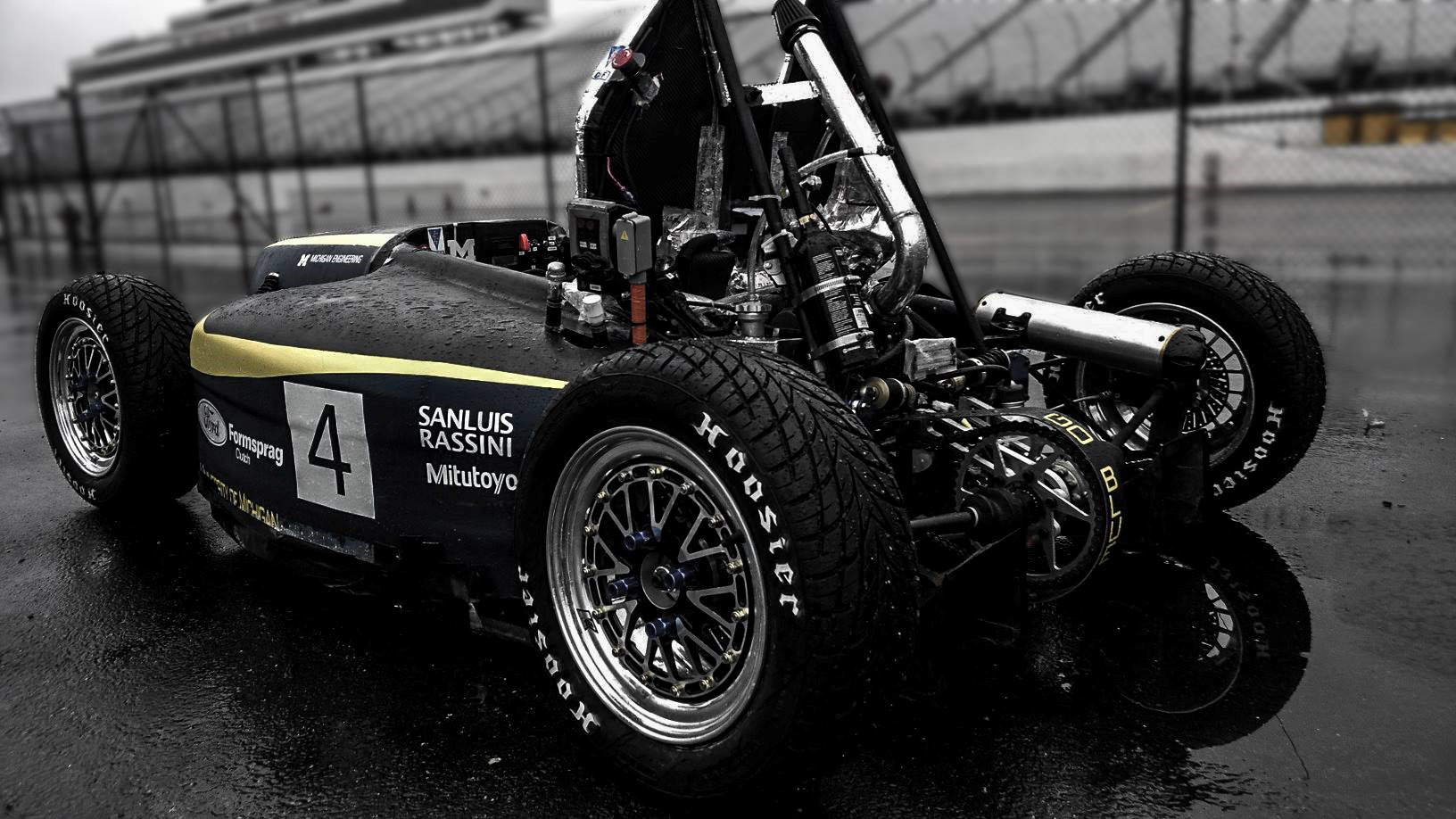
My role on the team was to designed and manufacture uprights for corner packaging and optimal suspension. This required collaboration with suspension, brake, and electrical system teams to ensure fit and function for each group. The uprights on MHR-14 were designed to efficiently package all in-wheel components, allow the suspension to be tuned via camber and toe changes, and steer the vehicle. I designed them in Siemens NX 8.5, and FEA was run using ANSYS Workbench 14.5.
Due to manufacturing constraints, the uprights were created with steel sheet metal components welded together. The sheet metal pieces were sent to be laser cut from a sponsor to ensure precision. Whilst it was being cut, I designed and manufactured the jigging for welding the pieces together. It took two weeks to weld all four uprights. Later in the semester, I had created spares as well should anything go awry on the race course.
The uprights were completed on time for all components to be mounted on the vehicle prior to the unveiling ceremony. This also allowed us to stay on schedule for testing.
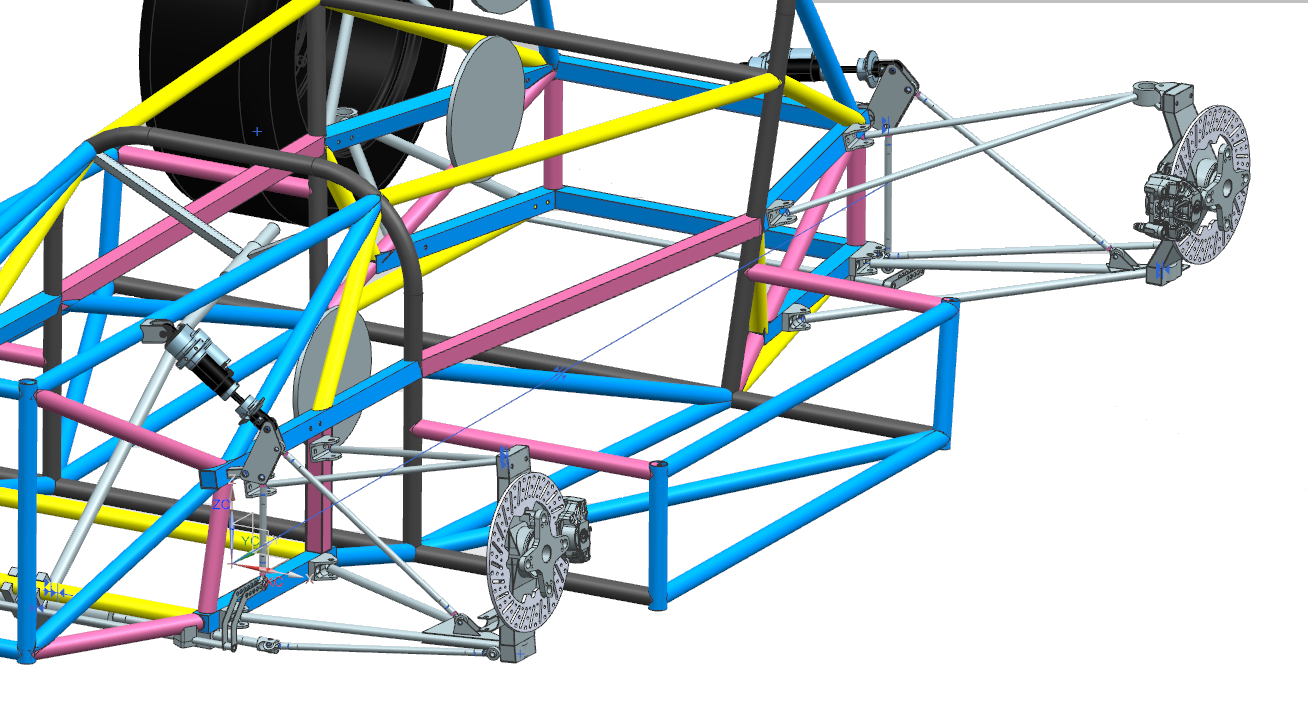
Corners assembly on vehicle w/o wheel
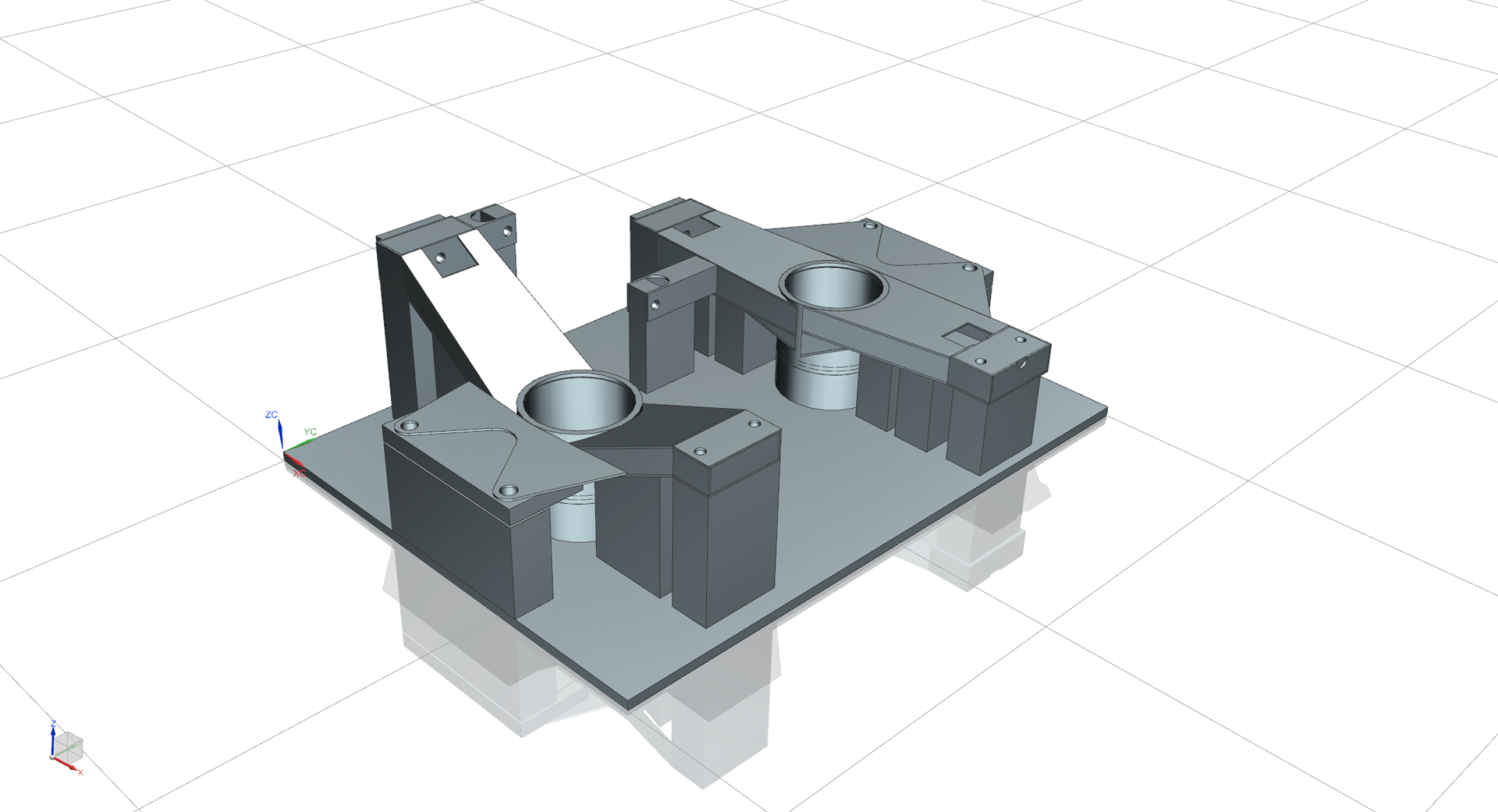
Corner sheet metal components in jigs to be welded
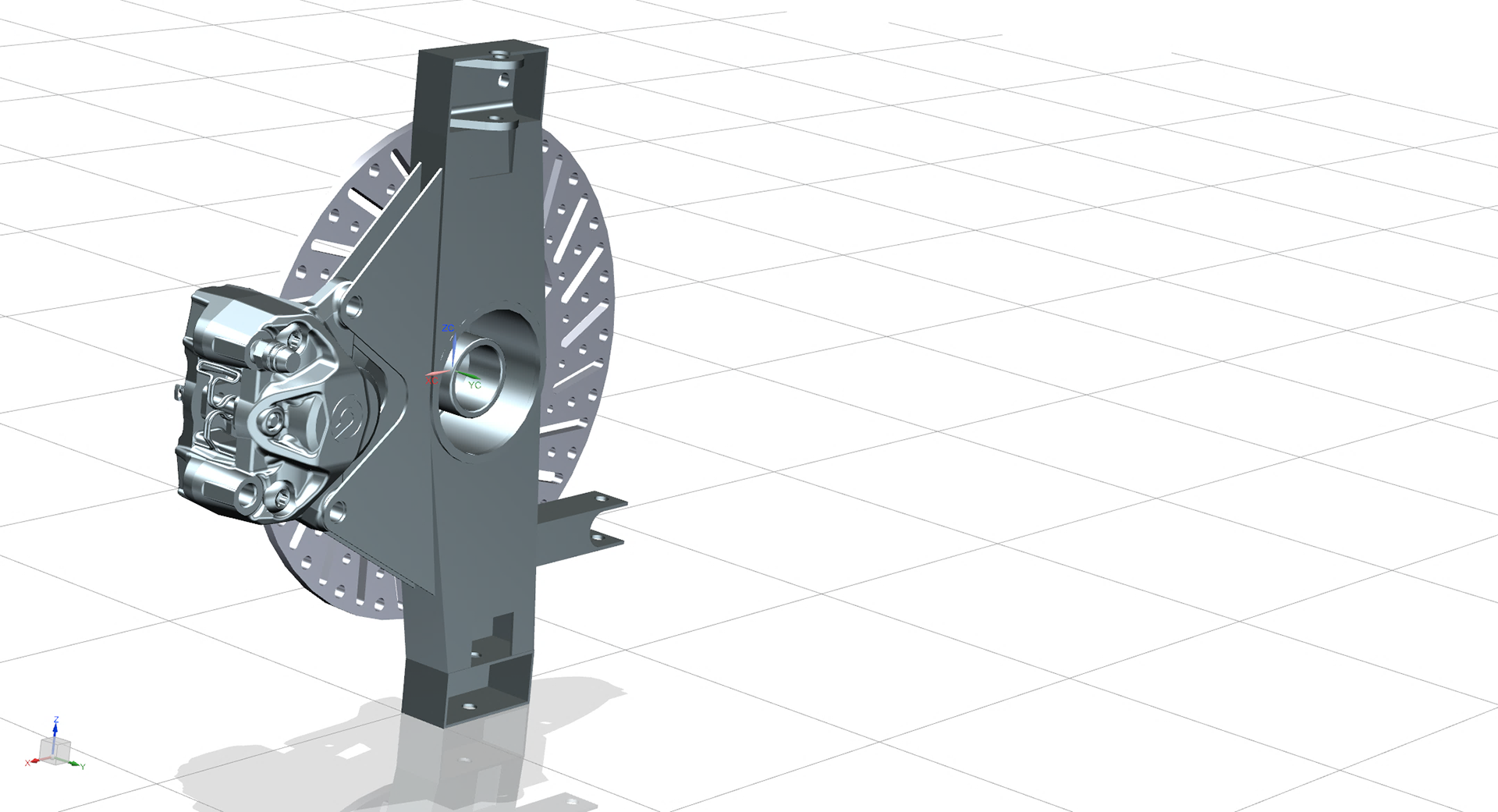
Inner view of corner assembly w/o wheel
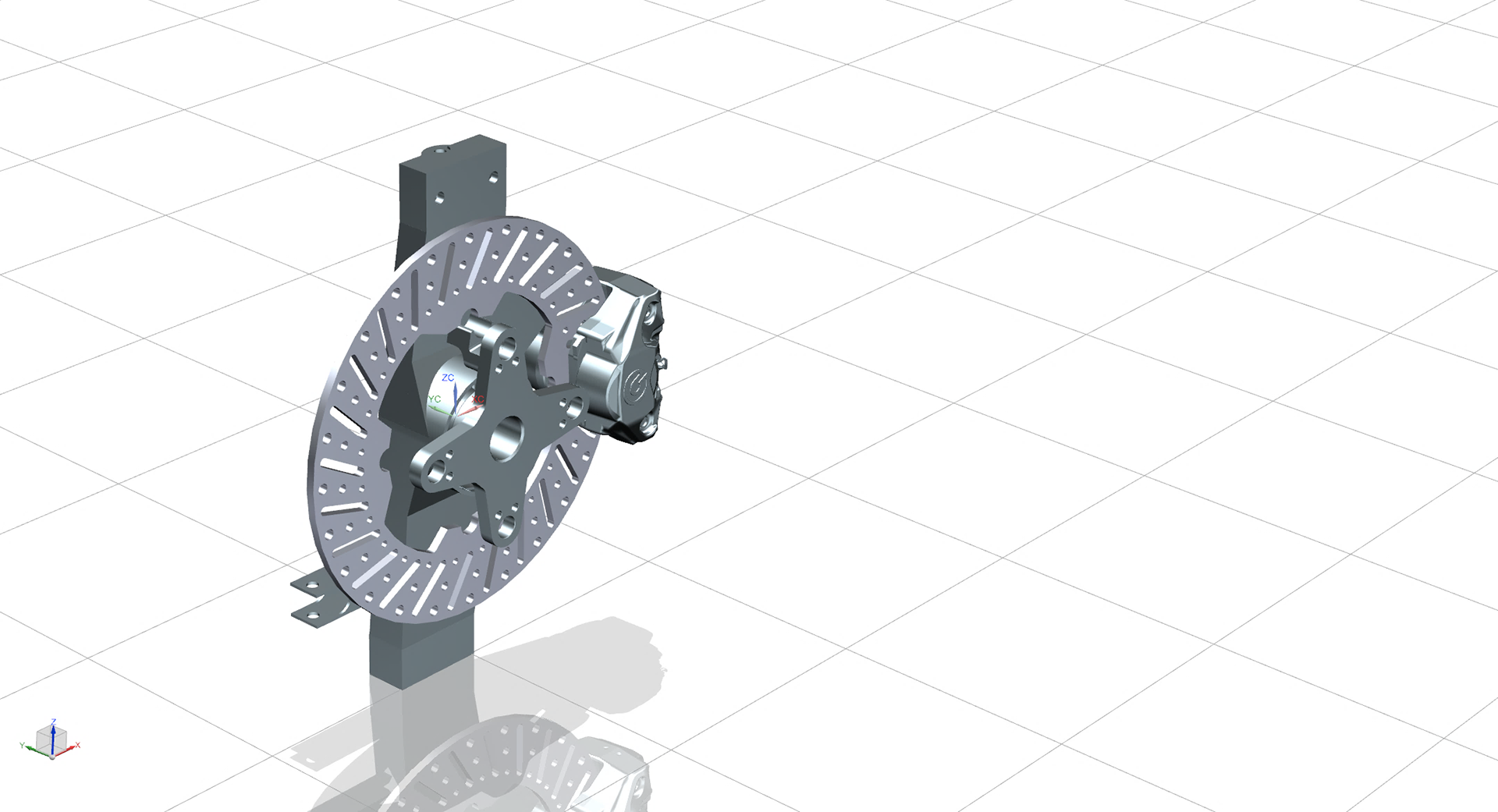
Outer view of corner assembly w/o wheel
In addition to designing the uprights, I was also the leader for team sponsorship and funding. I spent a lot of my time leading a small team to cold-call various businesses around Michigan for manufacturing/resource support, as well as companies nation wide for product and monetary donations. In 2014, we received the most sponsorships ever since the team's start, with donations in excess of $65k. My personal proudest contributions were Molex, who gave us electrical connector support and raised their monetary donation from silver to platinum sponsor during my 3 years on the team, and Mitutoyo who donated high precision measurement equipment for machining.
I was also in charge of creating the media marketing for the team, including photography, filming, and editing for our season.
Key Takeaways:
• "Design, build, test" mantra and putting into action
• Working under extremely tight deadlines and pressure
• Failing quickly and often to learn as much as possible
• Extensive manufacturing / machine shop experience
• Cross-functional collaboration between many engineering factions
• Traveling to competition to witness hard work be put to use
• Videography/photography experience with Adobe Premiere for team promotional media