During my 6 months I was tasked to create a Pen Design Guideline and work on a Parker Jotter click project. The Parker Jotter project was to isolate click scratchiness and make a recommendation for a solve, as well as explore potential new sounds.
Completed sound box in its open state
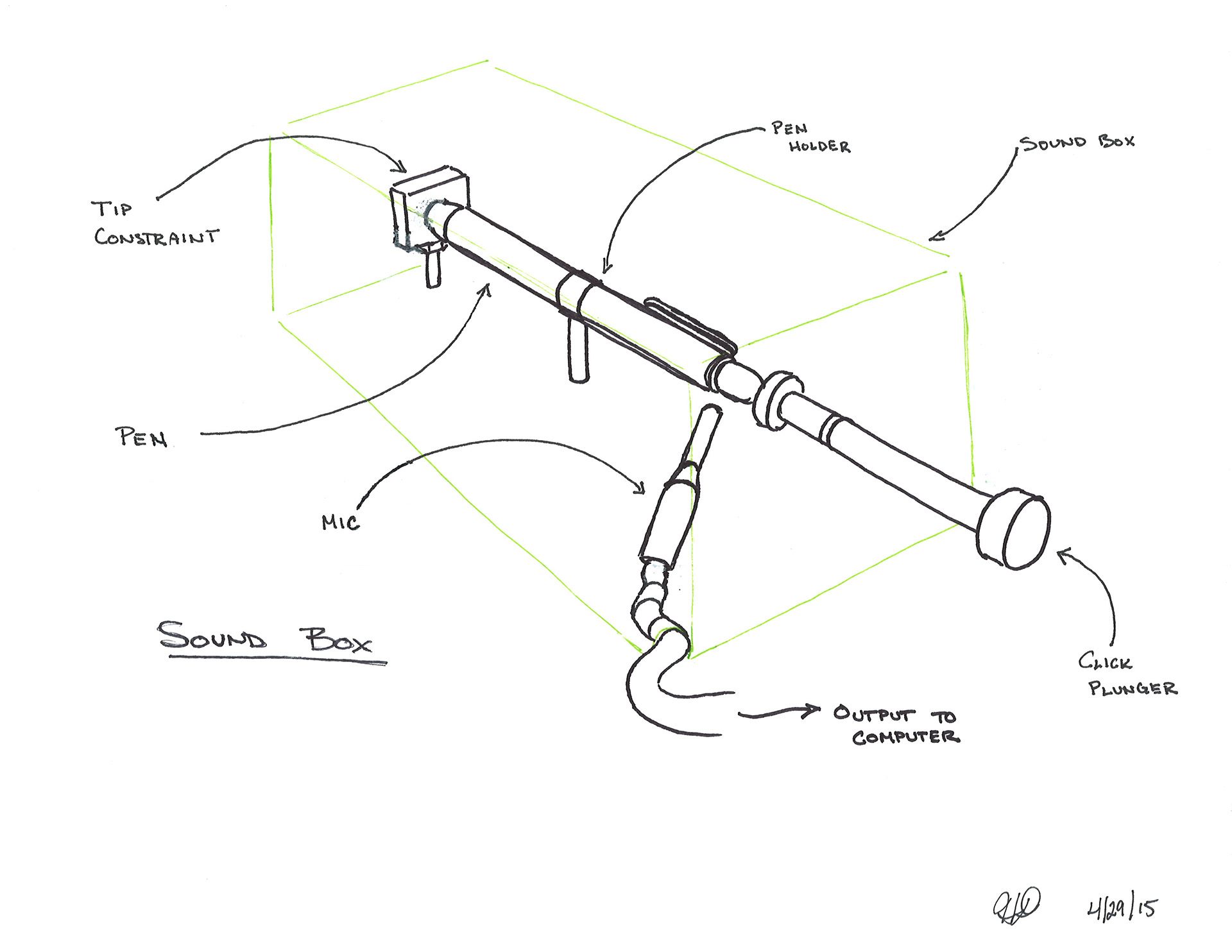
Original sound box concept sketch
To begin exploring click sounds, I needed to gather accurate recordings. We didn't have an anechoic chamber or recording facility within the company, so I decided to create my own pen-sized, semi-anechoic chamber.
I used my textbook from my Acoustics Engineering course in school to gather a list of accessible materials with sound absorption coefficients that best suited their role. I constructed the box with 4 layers of materials: plywood, cork, mass-loaded vinyl, and acoustic foam.
Plywood: outside layer, absorption coefficient is very low, reflecting outside noise from the system
Cork: layer was used because it has a good absorption coefficient and adheres well to wood
Mass-Loaded Vinyl: helps to keep external noise out, and can help reduce echoes from internal noise
Sound Absorption Foam: the most absorbent material for damping reflections that might get recorded
The mass-loaded vinyl was an idea I got when watching home construction videos for soundproofing basements. It's very thin with an extreme dB reduction rating.
A 2x2 alternating foam design was seen in many current studios, therefore I thought it would be advantageous to try. I carefully cut and placed foam pieces in alternating vertical and horizontal fashions to create as many sound traps as possible. The foam would keep the same absorption characteristics I'd get if they were not alternating, so there was nothing to lose when it came to trying the alternating pattern.
In order to position the pen inside the box, I created a clamping system to be able to fit any size writing utensil (marker or pen). The universal v-clamp was used because diameters of writing instruments can very, and the tip holder needed to be able adjustable vertically. The barrel holder needed to be adjustable horizontally because lengths can vary.
To minimize interference with the recording, I conducted the click actuation via rod through a vibration damping, bronze bushing press fit into the box. The rod had the capability to be attached to a force gauge to ensure consistent click force.
The force gauge was attached to a sliding rail system to keep the rod alignment with the pen. A future improvement would be to have a stepper motor controlling the force gauge so I can keep a consistent click speed, as we do for our laboratory click force qualification testing.
Equipment:
• dbx RTA-M reference microphone
• M-Audio M-Track Plus USB interface (with built in phantom power for the microphone)
• Adobe Audition
When setting up the recording, the box was able to open on hinges from both the top and the front for easier access and placement. A slot was cut in the front of the box for the XLR cable to run through. The box was held tightly closed using draw latches. Stickers were placed on the base of the box to have consistent mic placement when comparing the same size pen, and the angles of the microphone stand relative to the floor and to the feet were marked to ensure repeatable placement should we need to move the box.
Performance
The box did an excellent job of shielding the microphone from outside noise, however it did pick up a constant tone of air circulation within the box. If we had access to MATLAB, I would have recorded the air noise and inversed the wave to create a band-pass filter. However, because we were only comparing apples to apples, and not trying to find the most accurate sound for the Parker project, I had figured the noise being present in both recordings would be OK.
Plastic Barrel Jotter
Stainless Steel Barrel Jotter
Results
I found that the scratchiness was coming from the pen refill rubbing on the new stainless steel barrel. The tip of the refill was not concentrically aligned with the end of the barrel, causing contact. My recommendation was for a molded alignment cone at the bottom of the barrel, which is already a part of the resin variant.
Thought process:
Looking at the visual FFT graphs, the stainless steel Jotter (left) was clearly scratchy compared to the resin Jotter (right), with fluctuations at different frequencies throughout its recording. Since there is no discernible frequency at which the fluctuations start or finish, and the amplitude is relatively lower throughout the entire spectrum, I estimated that the scratchiness came from components in constant contact. Since the caps and uppers are the same for both pens, it helped deduce the location of the scratchiness coming from the ink refill. Since the refill is standardized, it must be contacting the barrel where the resin variant cannot.
Future Research:
It was decided that research to design a signature click was not an immediate need and therefore was denied further funding and exploration.
It was decided that research to design a signature click was not an immediate need and therefore was denied further funding and exploration.
Key Takeaways:
• Hands on with idealistic sound research
• Building a test structure with the intent to collect data for future projects
• Process of going from idea, to sketch, to pitching the idea, to a built device