As a Studio Engineer, our role is to assist the Industrial Design and Usability teams with upfront concept development, as well as any fixturing or prototyping for various studies and/or photo shoots. We can be roped in early for full mechanism development, or very late for quick iterations that a design engineer may not be able to tackle given such a short amount of time. All CAD, prototyping, and assembly is completed in house.
Here, I show two different projects I worked on during my time.
Levolor Blinds Usability Fixture
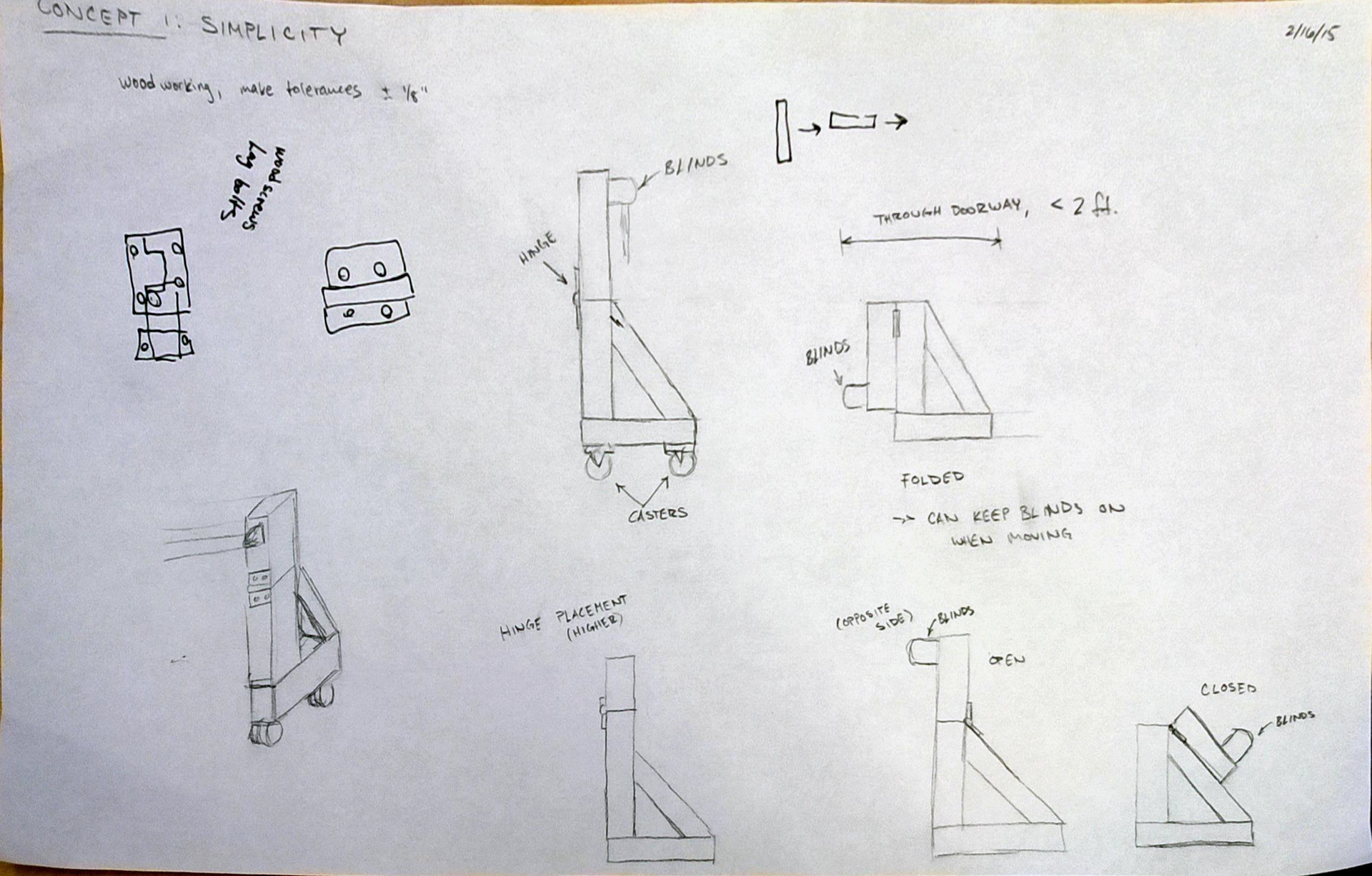
Concept to CAD to completion of the blinds test fixture
I was tasked with creating a test fixture for a usability study to evaluate different blinds mechanisms.
The requirements included:
• Proper window height (~6ft)
• Has wheels to assist in moving
• Can fold and stack for easy storage
• Sturdy enough for regular blind use
• Can integrate load cell to find max force during interaction
• Under $500
This task began with sketches and sourcing of material. Once costed out with a BOM, the project was sent to the Usability team to review and approve the funds. The total cost of three fixtures was only $343.61 and only took 3 weeks from beginning to end, including manufacturing and assembly (completed by myself as well).
________________________________________________________________________________________
Rubbermaid Commercial Access and Mobility Prototyping
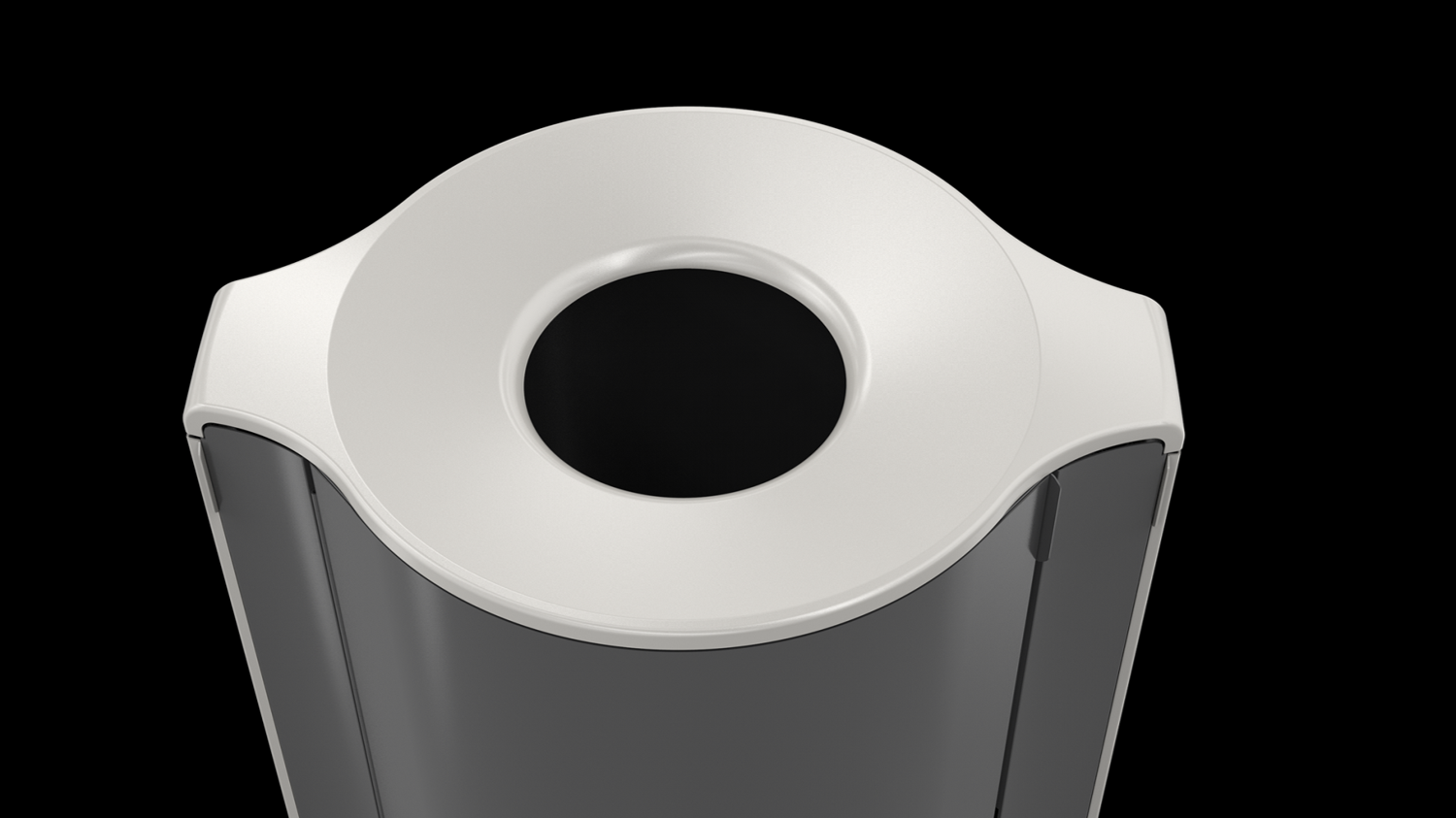
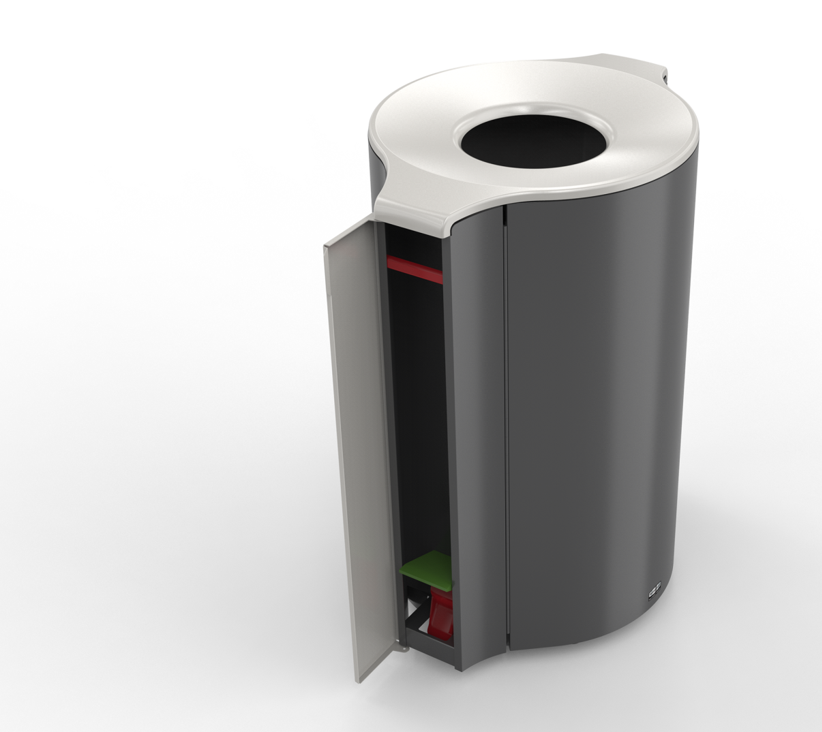
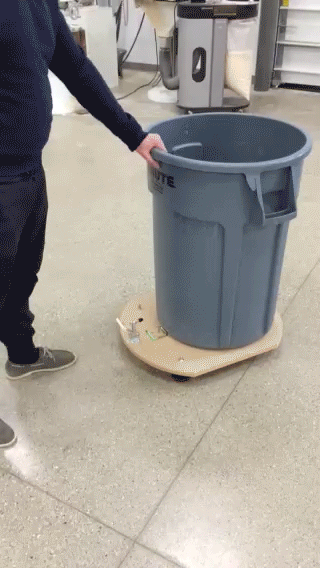
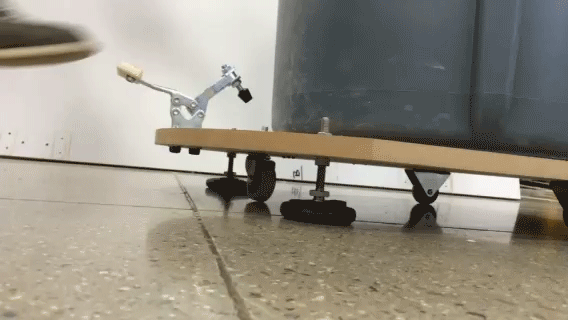
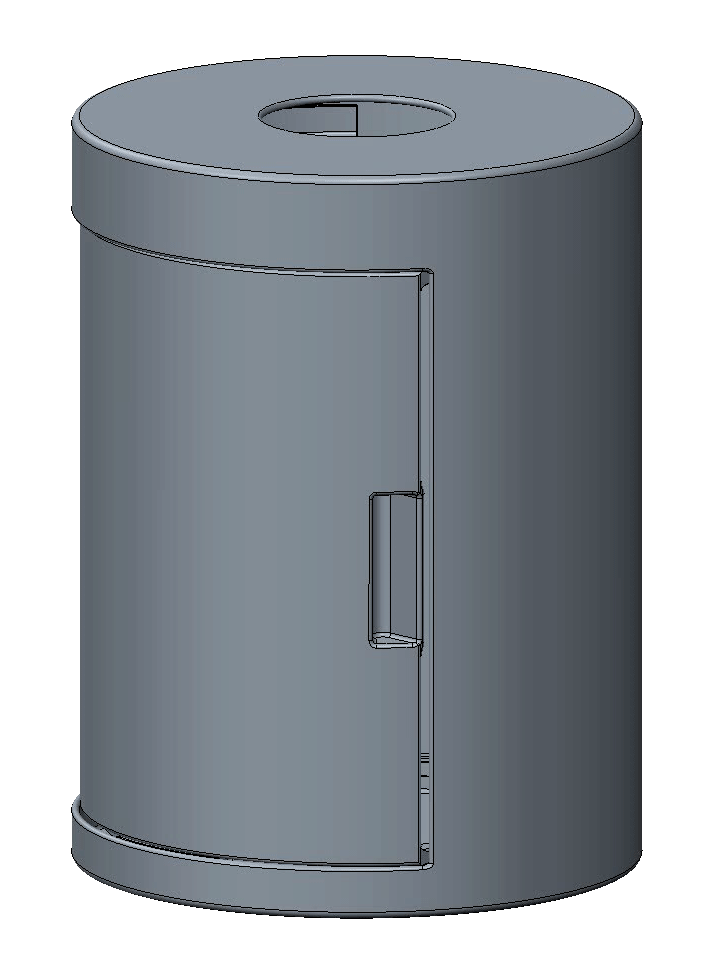
The Rubbermaid Commercial team was designing trash bins for high traffic areas such as airports, business lobbies, and arenas. These bins needed to be very large in capacity, whilst also being mobile when the space changes or to change the receptacles without being in the middle of foot traffic. Once ideas were brainstormed with the industrial design team, we conducted many mock prototypes, and were able to create some unique solutions for both mobility and access.
Mobility - The trash can needed to stay stationary when in use, and transform to become easily maneuverable by stepping on a pedal. I concluded that 2 wheels and 2 rigid feet were sufficient to prevent unintended movement under the empty can and projected enclosure weight. I then prototyped and concluded that the can just needed to deploy one wheel below the rigid feet to allow movement.
Access - The selected concept to execute was a van door. We wanted the custodial staff to be able to slide open the door, rather than open a standard steel door acting as a huge cantilever. We observed that the cantilever doors were often used to help maneuver the trash bins, which increased wear on the product.
My role was to create CAD mock-ups using Creo 2.0 of various ways we could achieve this. It was learned that in order for the door to be flush, it would need an inner offset before it translated along any rail system, and that structural integrity could be compromised due to the arc length of the rail.
Key Takeaways:
• Understanding what Industrial Design is and how designers operate
• Working side by side with ID and Usability teams to achieve their visions
• Daily Creo usage for extended periods of time and under tight timelines
• Continuous switching across projects and brands while being able to output consistently great work
• Making an impact on the office community through my creation of a recognition program